A Team of three Italian companies is involved in rethinking commercial aircraft's interiors for the benefit of passengers. Funded by the Clean Sky 2 EU program, the project includes transversal overhead lockers , baggage spaces under the seats and automatic touchless toilets. It is all made to improve space and comfort.
Planes cabins could soon be very different from those we are used to. But it is well known that in aviation, innovation - before it can be available, leading new standards, must be validated from aeronautical authorities and must be tested for a long time. This is why Ratios was born. Funded by the European program Clean Sky 2, it encorporatesthe skills and experience of Leonardo, Delta Interior Design and Studio Volpi.
The idea is to completely rethink airplane cabins from the needs of various travelers: from those with childrens, to those with disabilities, but also improving the working conditions of flight attendants and increasing comfort for all. The project is not only about designing new seats, but it is also about creating different spaces for over head racks for storing carry-on baggage, reshaping common areas with fully-automated vending machines providing drinks and food. This is all made using new materials and technological solutions never tested before on aircrafts. For example, think about how more comfortable it will be to place our suitcase under our seat, or experience a completely touchless journey in the toilet because the wc opens and closes by itself, and it’s automatically cleaned and sanitized.
The companies involved in the project developed a creative, as well as innovative project, to address the economy class syndrome, considering that the average passenger size changes continuously and airlines require to use every space available in the cabin.
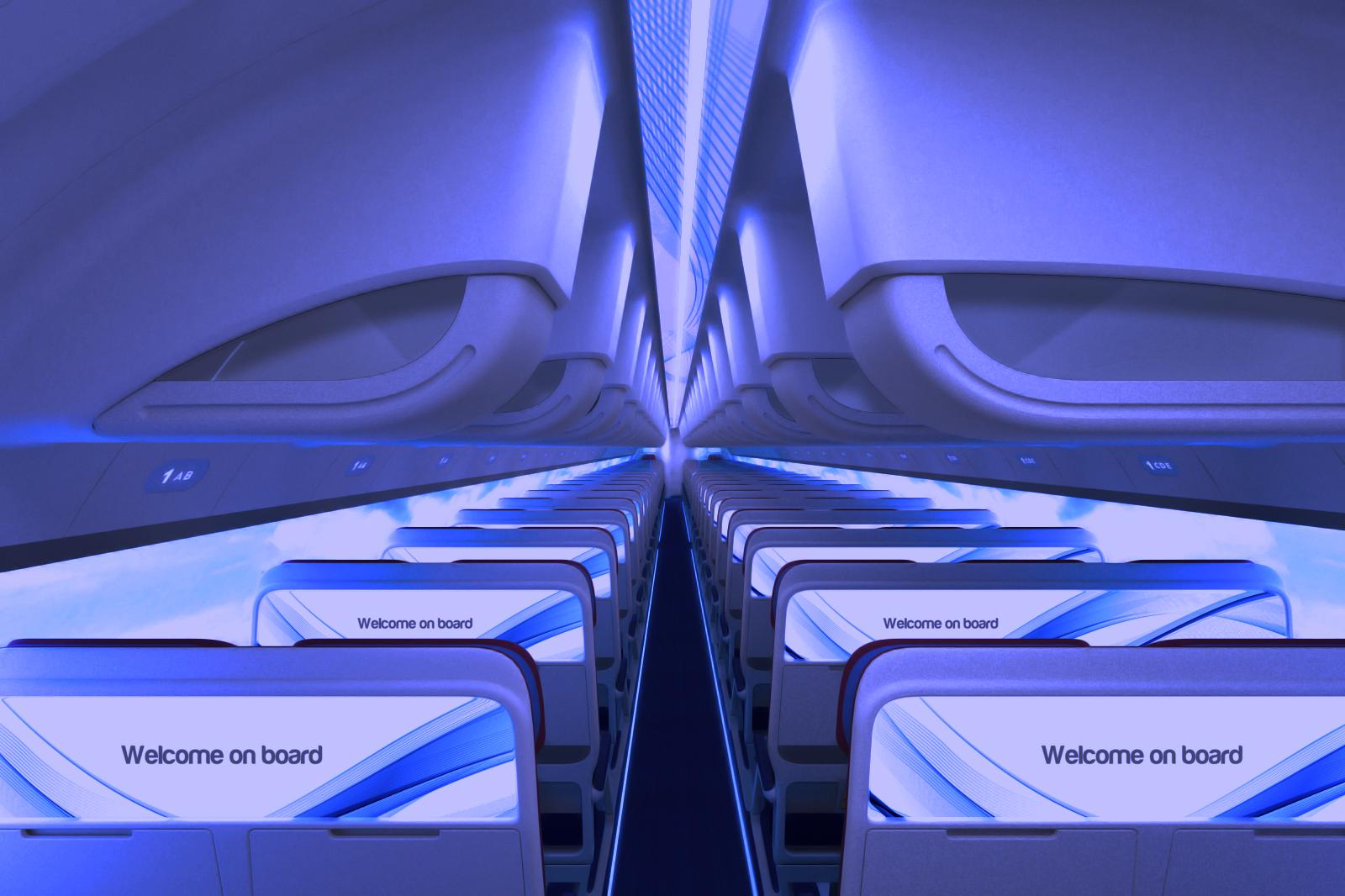
What would you think if, stepping on board of one of the aiplanes of the future, the overhead lockers were no longer aligned along the top of the fuselage, but they are transversally placed with an allocated space for each seat, and if the cushion turned, allowing us to stretch our legs with our belts fastened? Probably an umbrella should be put elsewhere, but it would mean no more fights to grab space for your suitcase and no more need of contortions on the seat. Regarding the new materials, Ratios Team studied composites but alsomodern fabrics which are resistant and light, with an eye on ecology, fireproof, easily washable, antibacterial and recyclable - when not produced from recycled materials.
Lately, we’ve seen many similar projects, but very few had any chance of becoming reality. While in the past we’ve seen improbable, if not impossible, solutions, the companies involved in Ratios maintained faseability focused on constructive solutions, and certification capabilities. "Not only we wanted to do something innovative, but also we wanted to save weight and reduce production times, while strictly respecting the parameters imposed by the aeronautical certification standards for seats, furnishings and components" explains Matteo Bulletti, aeronautical engineer and managing director of Delta Interior Design "Especially after the pandemic, it will be very important to guarantee safety and hygiene on board of aircrafts. New technologies allow great margins for improvement, such as touchless toilets that avoid contact with parts potentially exposed to bacteria".
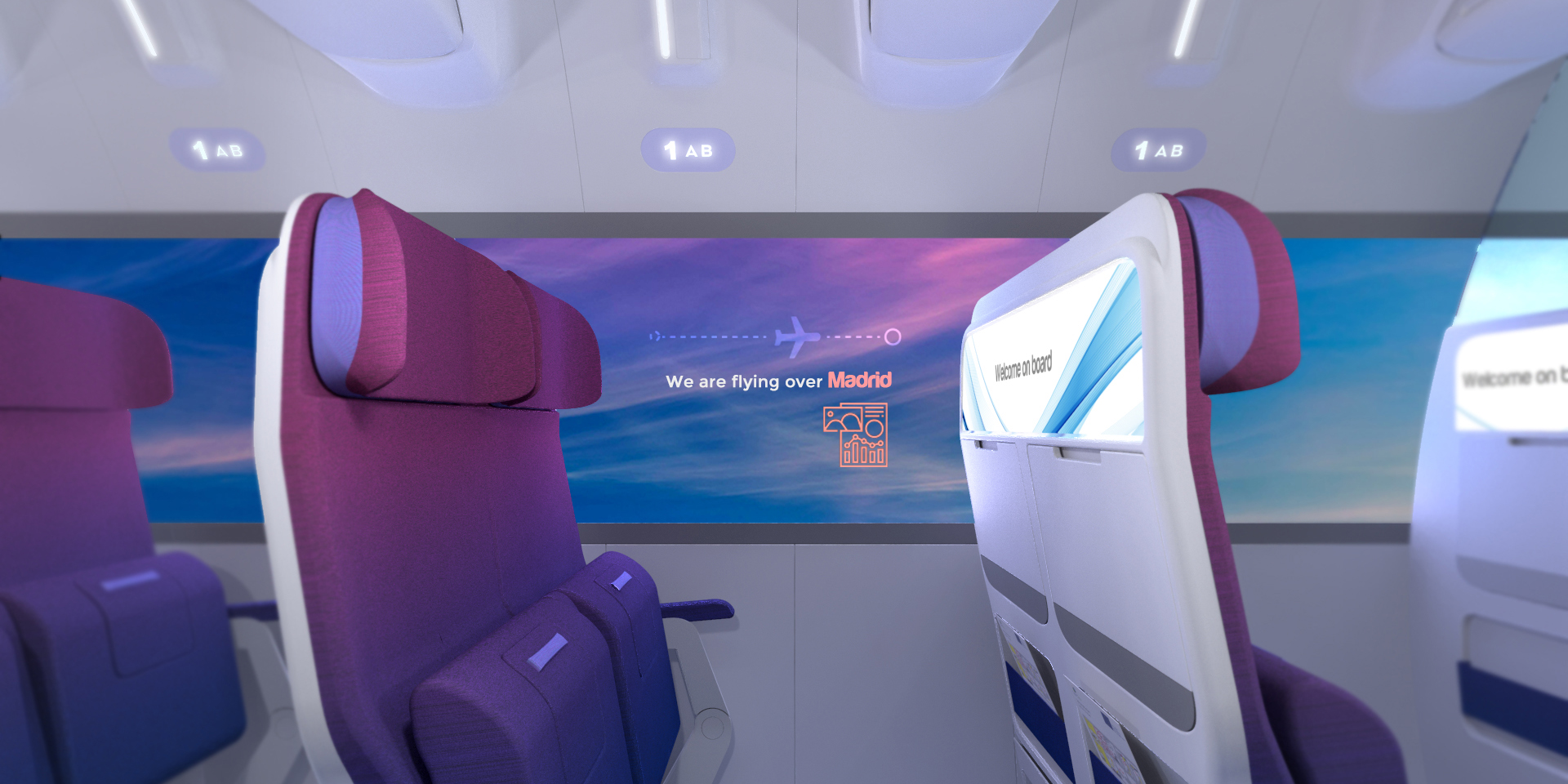
"Not only we wanted to do something innovative, but also we wanted to save weight and reduce production times, while strictly respecting the parameters imposed by the aeronautical certification standards for seats, furnishings and components"
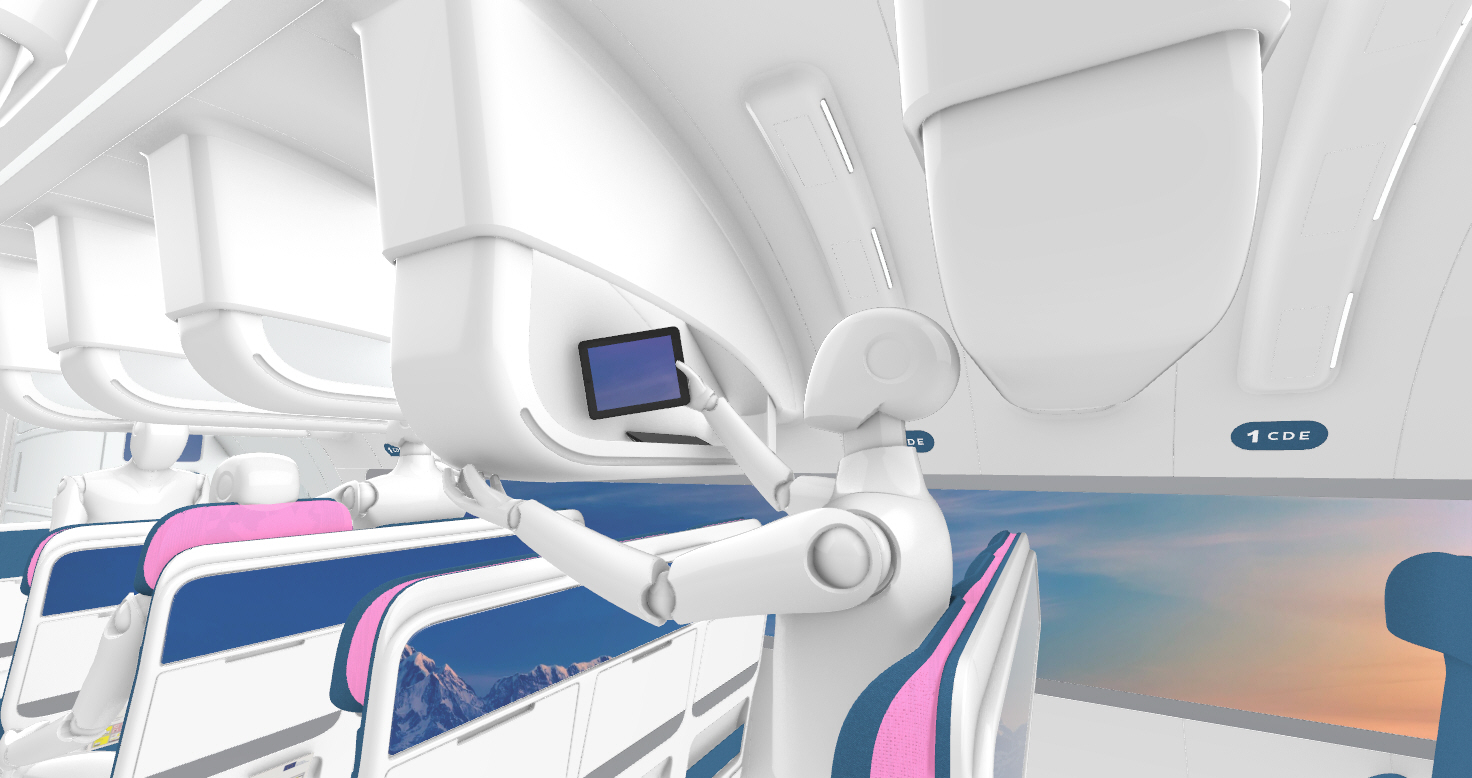
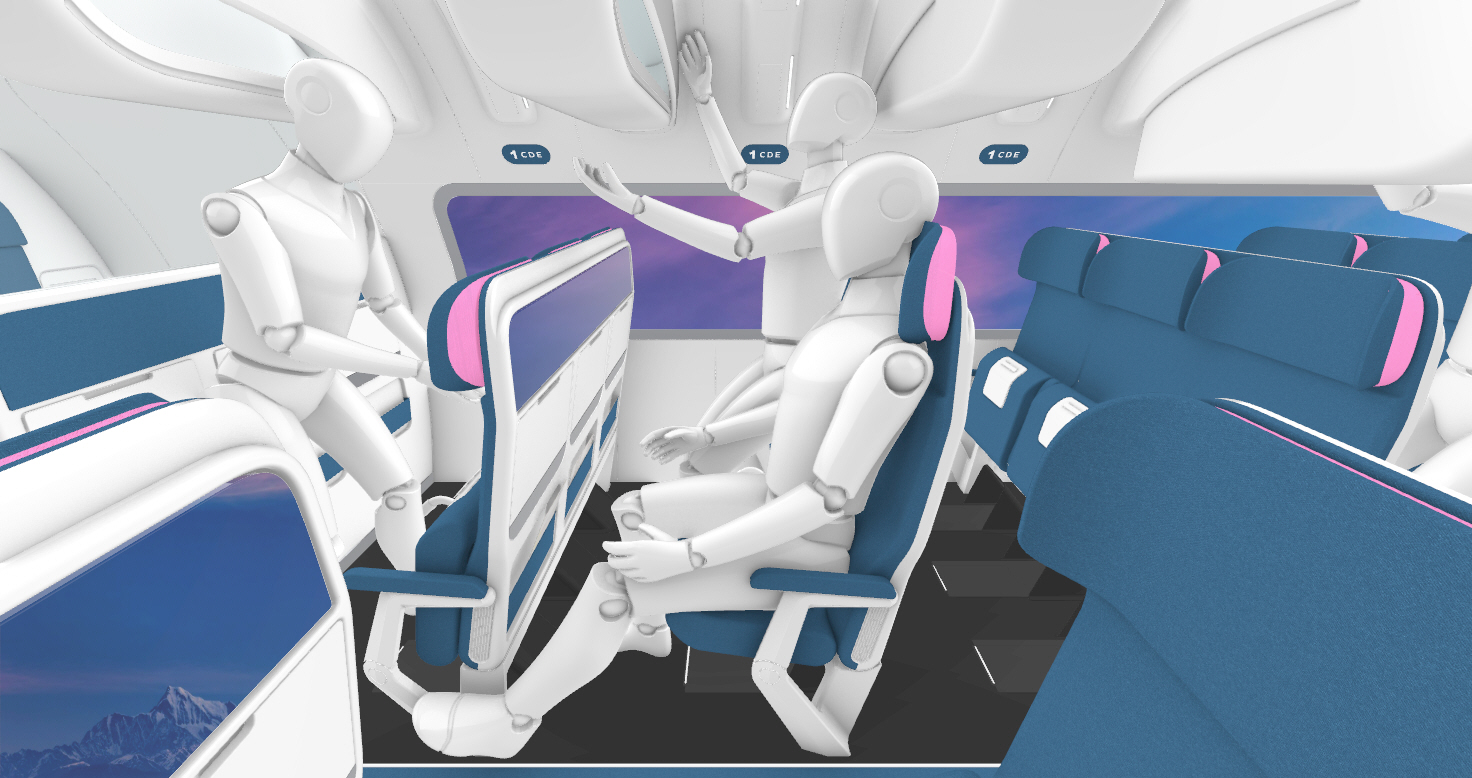
Moreover, from a regulations point of view, both the European Aviation Safety Agency and the Federal Aviation Administration impose to achieve the ETSO/TSO certification, and to demonstrate that, in the event of a crash, the seat belts support the passenger standard weight (required by Cs-Far 25.785). The seat dimensions and the inclination of the backrest are also regulated as well as the resistance of the seat structure that should absorb loads up to 16 times the force of gravity. The electronic entertainment system is going to be improved in the project, with larger and more curved screens, and also the safety of the overhead lockers, which could be opened and closed with your smartphone. Also the area where the food is stored and prepared, will be improved to enhance the quality of the flight.
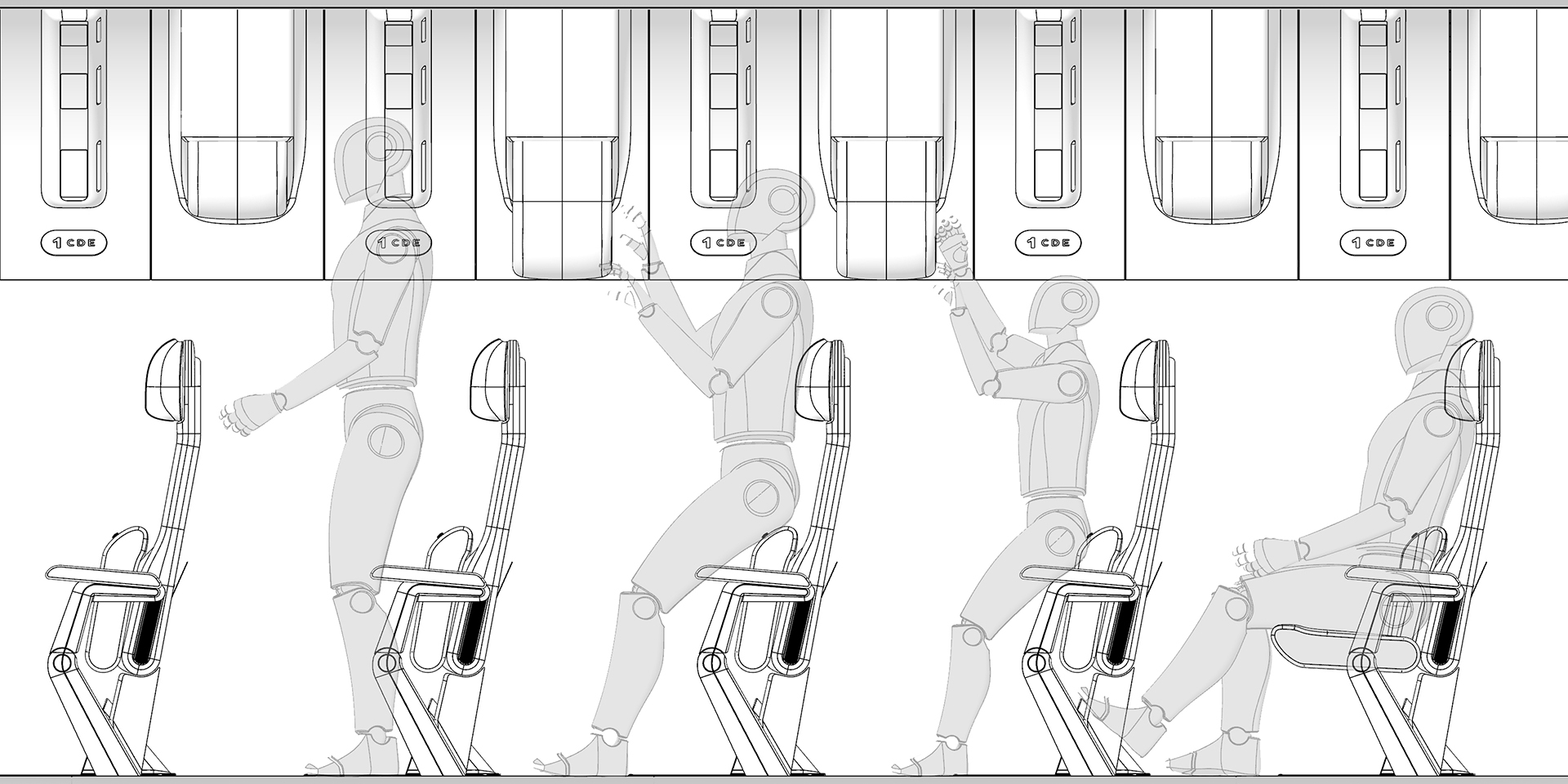
Considering the job of flight attendants, Ratios team collected their feedback and worked on waste containersthat close and unload automatically, a toilet booking system that works through a mobile applications and the possibility to communicate with the crew in a more confidential and effective way. The results of the studies carried out by Ratios can truly lead to new passenger cabins, with sit rows positioned in a club-style orientation to make conversations easier and increasing legs space. Why not breaking the rigidity of the windows, which could be larger and also be repositioned to give passengers an enchanting view on the outside. And of course, it would give kids a less rigid and forced accommodation, which is often the origin of desperate crying.
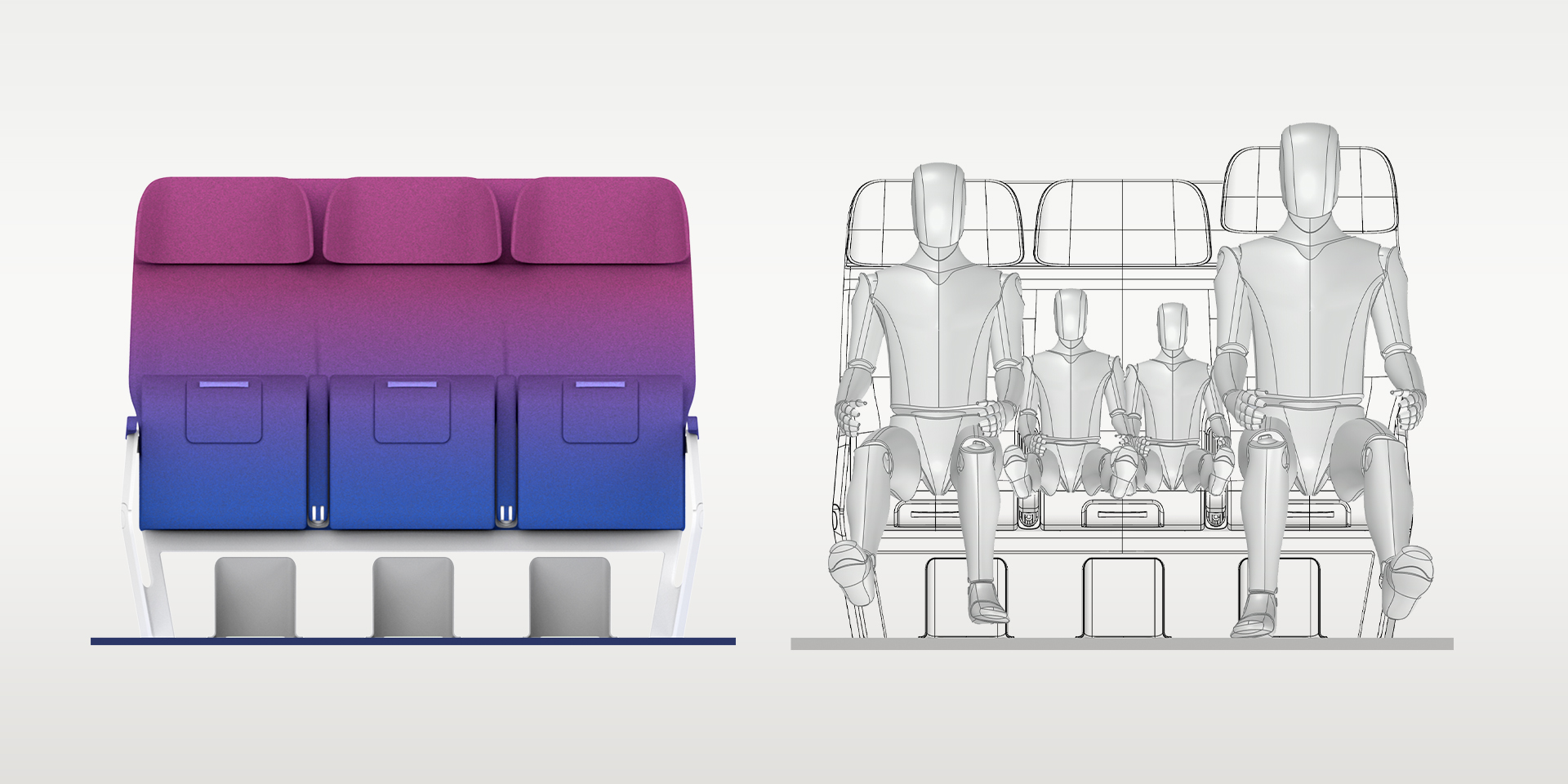
Innovative materials
To the research of new technological solutions has been added a research on materials. Typically, materials used for furnishing elements are divided into two categories: those that make up the structural parts, such as the seats frame, galleries, lavatories, and aesthetic materials, such as fabrics and cushions, also called soft-goods.
Ratios research followed the line described above (hard and soft goods), to evaluate all those new materials, sometimes already used in other fileds as automotive and construction. In addition to pure innovation, Ratios Team investigated different aspects that are often not taken into consideration. For example, in addition to the traditional evaluation parameters, importance was given to the search of materials with low or zero environmental impact, ecological, recyclable, sustainable.

As far as finishing materials are concerned, they focused on fabrics made with natural materials such as hemp and cotton - if not coming from intensive culture or treated with pesticides or fertilizers. For colours, efforts have been made to minimize the environmental impact of traditional chemical processes, also with an eye on energy and water consumption decreased by reducing the temperatures of the colouring process. The research explored the possible treatments for these new materials. In order to be installed on aircrafts, especially for passenger transport, all materials must demonstrate a high level of safety. In the case of non-metallic materials, such as fabrics, plastic laminates and composite, the main requirement regards their infalmmability: they must demonstrate a high self-extinguishing capacity, low emission of fumes and the lack of potentially toxic elements. Currently, there are treatments which, applied on fabrics and leather, allow to significantly increase their fire retardant properties. Once the new materials are tested following the standard rules, they will significantly increases the range of finishing that can be installed on airplanes. IThere are also treatments that, using nano-technologies, allow to increase the properties of hydro and oil-repellency and resistance to bacteriological and microbial contamination. These stain-proof properties contribute to reducing the washing and sanitization cycles of the seat covers, cutting the airlines managing costs o and significantly decrease the use of detergents, hence their dispersion in the environment.
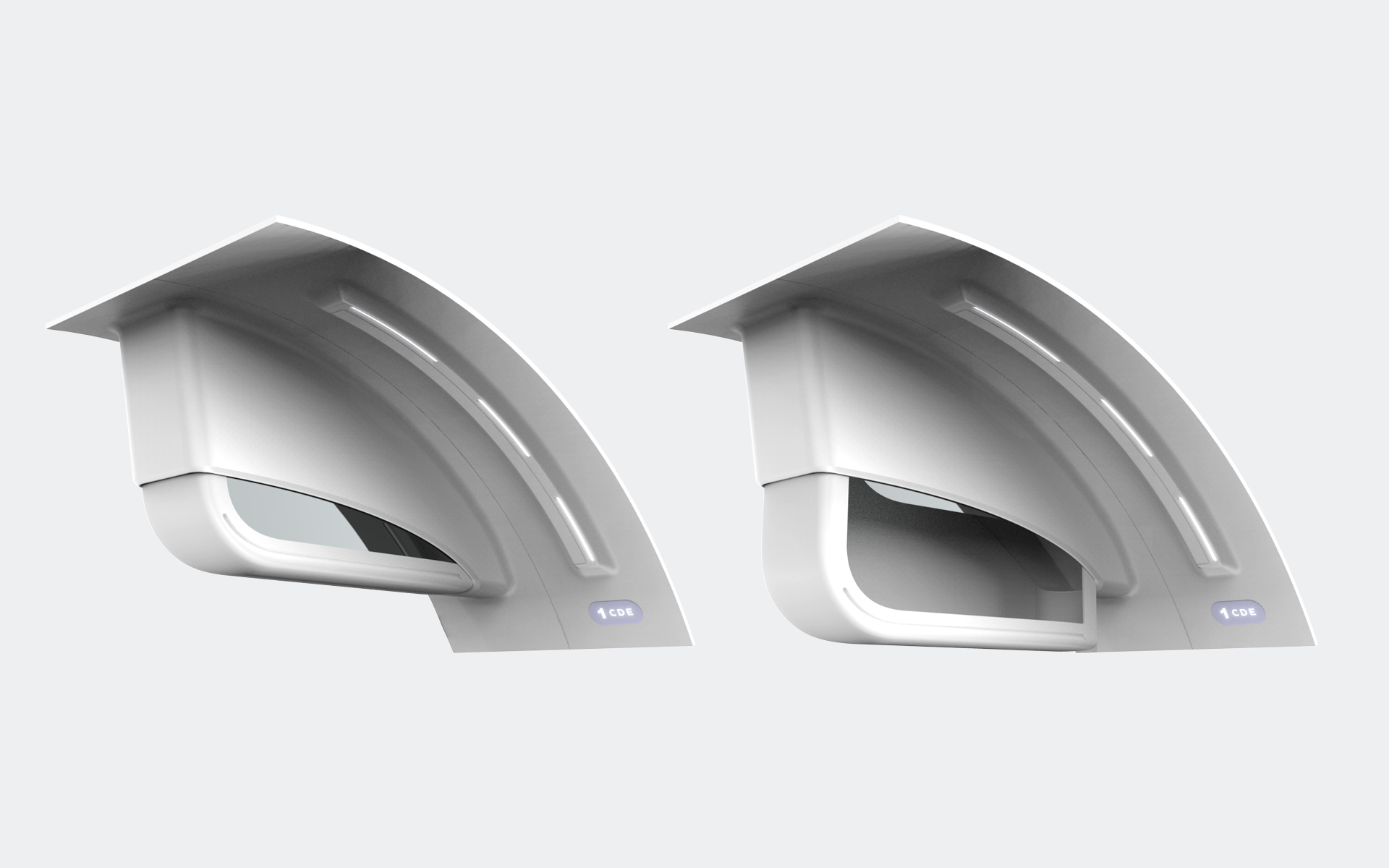
Regarding structural materials, the research demonstrates the possibility of using new polymers that have mechanical characteristics similar to those of the alloys currently used (aluminum), but with lower density. The molecular structure of the polymers can be modified according to needs, as shown by researches: the base polymer can be added with reinforcement matrices (e.g. glass fibers, carbon, boron), to increase its mechanical characteristics, or it can be mixed with other elements which can significantly decrease its density, with significant benefits in terms of weight but with no consequences on the mechanical characteristics.
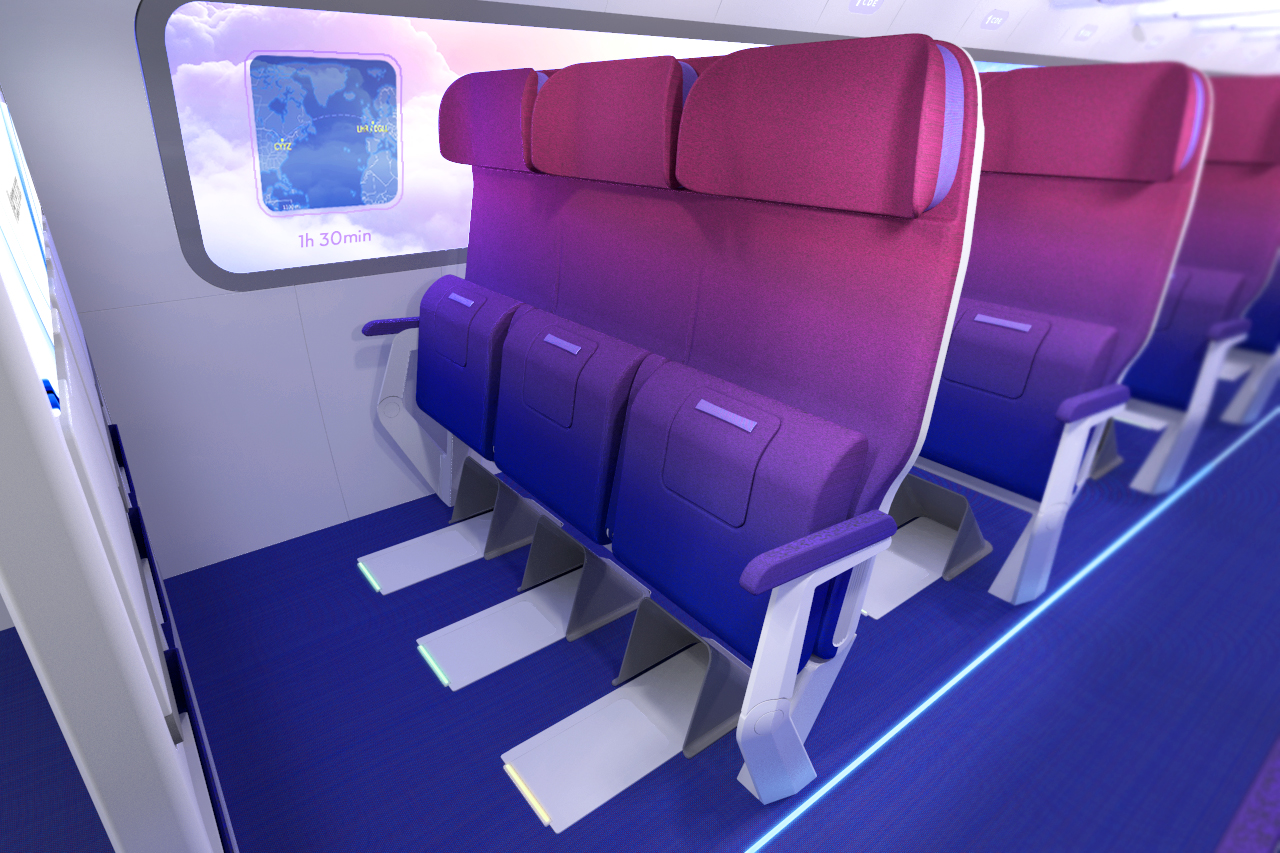
In particular, the use of microspheres (glass-bubbles) mixed in appropriate percentages with polymers (e.g. nylon, polysulfone or polycarbonate), can reduce the weight of the product up to 35% without significant decreases in mechanical characteristics. Note that the use of these microspheres does not require modification of the moldsin current use but, on the contrary, the new mixture improves the production process. Another interesting material is represented by a laminate obtained by placing layers of unidirectional carbon fibers. The resulting sheet combines mechanical characteristics comparable to the most common metal alloys (aluminum, magnesium), and the flexibility of thermoplastics. The thicknesses and orientation of the fibers can be designed according to the structural and dimensional needs of the foil.
This article was originally published in Italian by JP4 Aeronautica e Spazio on 11/11/2020 and it is written by Sergio Barlocchetti, who agreed on the publication of his content on our website and provided the English translation.
Watch the video to learn more about the innovative cabin experience.
-
-
-
Prospettive Mar 30, 2020
KITCHEN 4.0: HOW DIGITALIZATION IS CHANGING THE RULES
Technological updating and the integration of an interconnected soul are turning modern professional kitchens into a perfect example of the 4.0 industry, where the product and its super digital powers become a tool to improve working conditions, enhance productivity, monitor the processes to achieve better results and create new business models